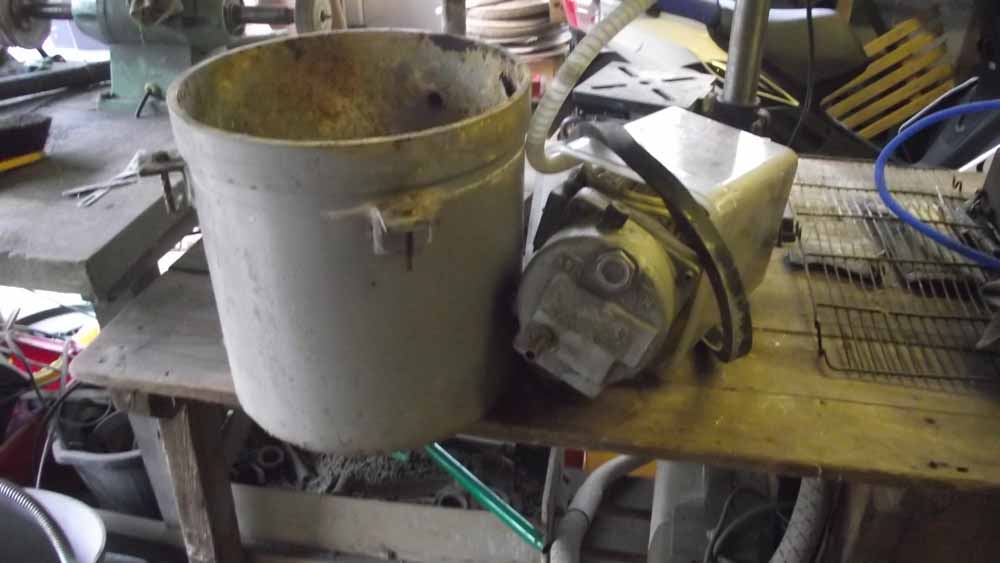
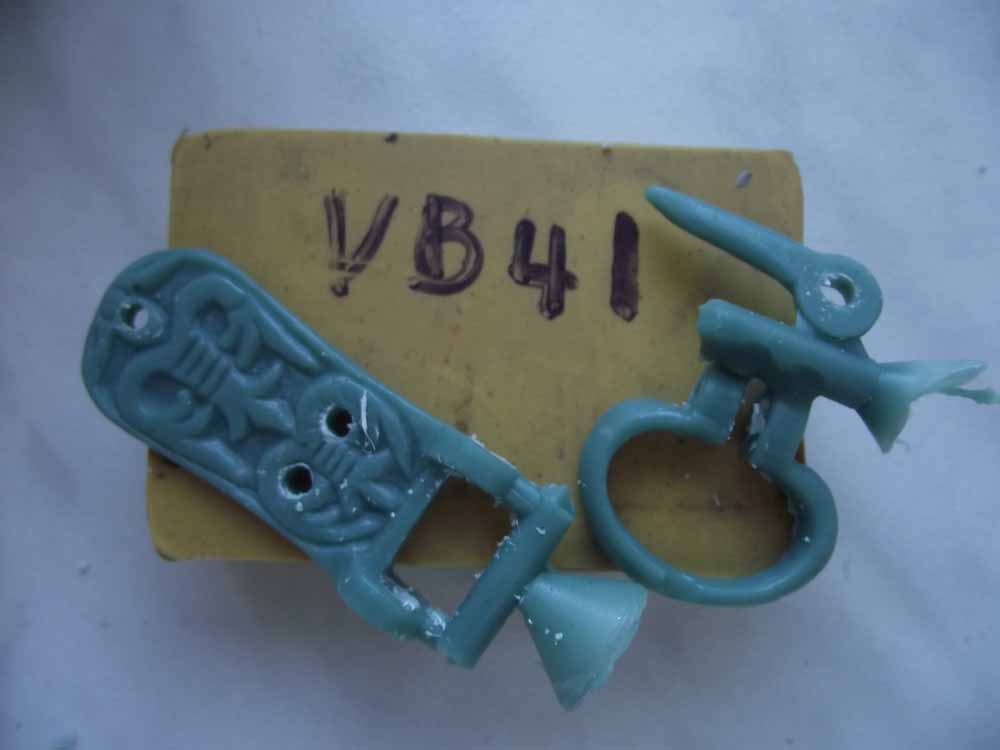
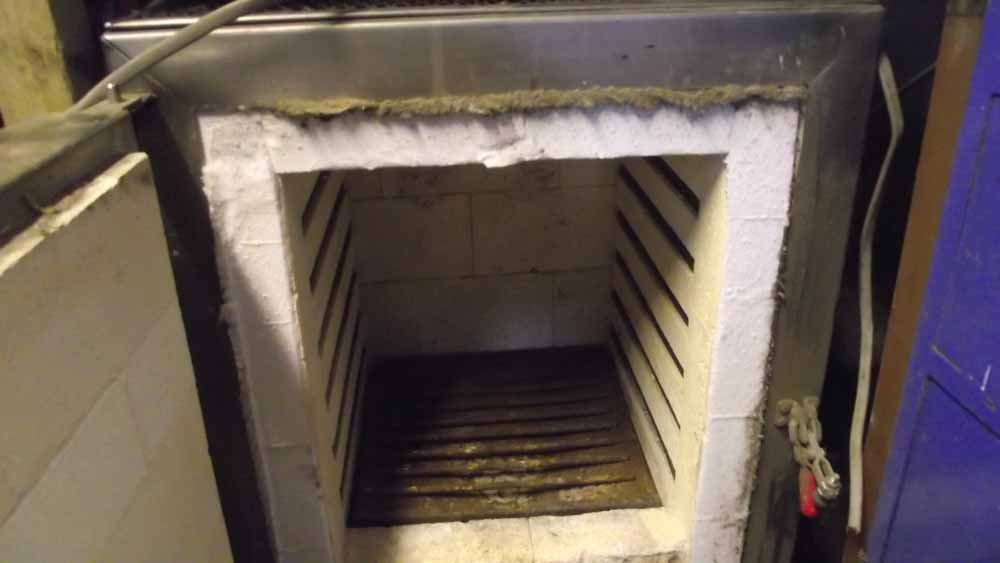
Lost wax casting is the process used to produce our re-enactment and historically accurate bronze and silver items. Each piece is individually made by hand. It is a long process as you will see from the information below.
1. An original needs to be found or a new piece carved to serve as the master.
2. This master is then surrounded with a special type of rubber and small tubes, usually of metal but can be wood, are attached to the master to enable sprews to be formed.
3. The master and rubber is put into a vulcanising heater and baked for a few hours at about 300oC.
4. The master is then carved out of the rubber with a sharp knife. It is cleaned of loose strands of rubber. The mould is now ready to have hot wax injected.
If only one item is required then it is possible to carve the piece directly out of wax but, the clue is in the name, this wax master will be lost in production and if the cast fails you will have to carve another one!
5. Wax is added to a pressure kettle and heated to about 80oC. The kettle is pressurised to about 1 bar and then injected into the mould.
6. The mould is then put to one side for a few minutes for the wax to harden.
7. The wax is then carefully pressed out of the mould. Many will be badly formed and rejected. The wax is not wasted as it can be added back into the kettle next time it is filled.
8. Many of the items (scabbard fittings are waxed in two parts, brooches need the catch mounts for the pins) need extra bits soldered on using a temperature controlled iron set at about 90oC.
9. The waxes are connected together into a ‘tree’ by using a soldering iron and sticks of wax.
10. The wax tree is put into a metal can and plaster of Paris poured in. This is done under vacuum pressure to ensure that the plaster flows and adheres to the wax so as not to leave any air bubbles that would lead to bad castings.
11. When the plaster has set and completely dried out the can is placed into a burn-out kiln where it is heated at 750oC until the wax has melted and passed out through the plaster. This is the ‘lost wax’ bit!
12. The can, whilst at a temperature still hot enough to stop the bronze from setting in the top of the tree, has the hot metal (bronze, silver or gold) poured into the top at about 1000oC. Under vacuum pressure the metal is forced down into the finest and smallest parts of the empty tree.
In modern days we use a vacuum pump but originally it would have been in a bucket on a very long rope swung by a very strong man for several minutes so the centrifugal force would push the metal home. I am not that strong or have the space to do it the old way!
13. The can is then left to cool, usually overnight and then the plaster needs to be chipped and blasted away.
14. The resulting metal tree is then dismantled with an angle grinder and tidied up with a linishing belt bench grinder.
15. The separate pieces are then placed into a vibrating polisher with a soap and grit to remove the worst of the muck, for about 3 hours.
16. They are washed and put into a second tumbler with an acid wash to clean, polish and brighten the metal. Again for about 3 hours.
Originally the pieces would be put in a basket in a fast flowing stream.
17. They are then dried and hand polished to protect and finish the item.
18. If it is a brooch or buckle then pins must be attached.
So, if you wonder why they cost as much as they do, now you know!
Paul Craddock (Druid)
www.re-enactment.com